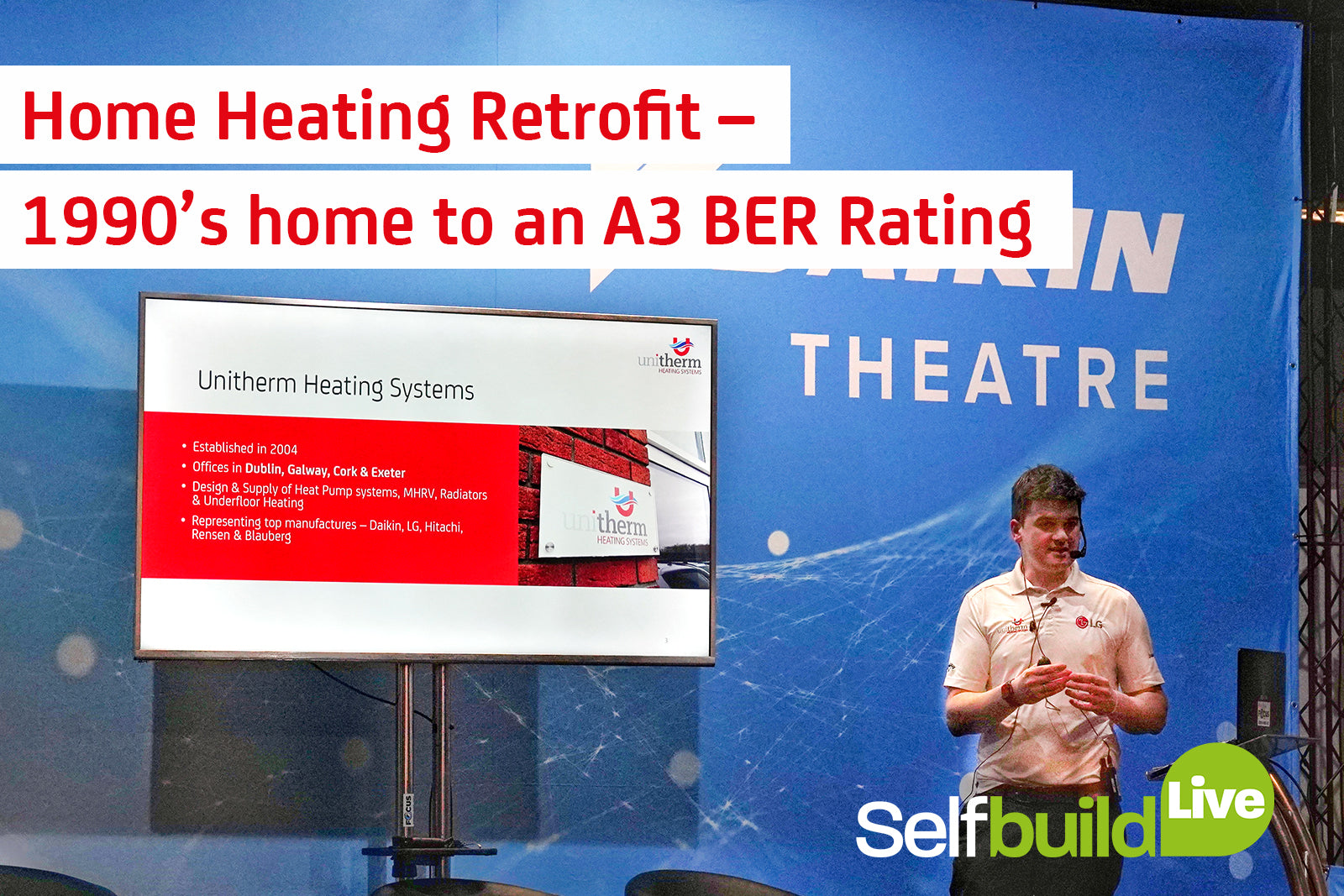
Home Heating Retrofit – 1990’s home to an A3 BER Rating
This retrofit is very close to my heart because it is my own retrofit. I can tell you about all things retrofit and the level of involvement it took to get the house from where it was as a D1 right up to the A3.
The following is a typed version of Adam’s seminar talk at Selfbuild live Dublin 2022. See full video here
Unitherm Heating Systems
Bit about the company first and foremost. We were established in 2004 as a supplier of underfloor heating systems. Eventually we progressed where we were doing our underfloor heating systems with different heat sources be it oil or gas boilers back in 2007/2008. Then at that time regulations began to change and heat pumps became more prominent. As a result of that our heat pumps began to be designed in conjunction with our underfloor heating systems.
We have offices in Dublin, Galway and Cork and just last year we opened a brand-new office in the UK.
And just to give you an idea of what goes on, in terms of the different markets - Ireland at the moment for heat pumps is predominately all new build, where as in the UK its predominately all retrofits. So, it’s a big different shift in terms of the market and how we go about things.
In relation to what we do, we represent many manufactures so we have a solution for pretty much everything out there and were not trying to shoehorn a solution with one manufacturer to make something work. It gives us flexibility that when we look at your project we can come back to you with a very bespoke design that’s suitable for your project.
We’re very engineering and technically biased, although we sell heat pumps the majority of people in the company are actually mechanical engineers, plumbers, electricians and refrigeration guys.
It’s really important for us that every system we supply out there in the market we can stand over. A big thing now at the moment, particularly for people doing new build is certification. Which is something that we offer as part of our package should you go with a Unitherm system. As well as that with a retrofit the paperwork now that is involved with the SEAI for the grants has quite a bit of work involved and we would do that paperwork for a lot of the contractors.
The Process
So, what do we do when you initially engage with in relation to the design? We will take your plans be it a retrofit or new build and we will design a system for your house as if we were the mechanical engineer on the project. We treat each project on a bespoke basis so the solution will be tailored for your own project. Once we do the design and get the go ahead from you, we then supply the products to the project and work with the installer who’s doing the job and fitting the job. In terms of technical support, we’re there when they’re doing the installation. It really is a peace of mind thing, should there be an issue with wiring, or something on site that needs to be changed or looked at, we actually have that flexibility with our engineers in the office to do that.
Once the system is then installed we offer a full commissioning service. Once the system is fitted, the commissioning is really important because we’re making sure the system we designed for you is fit for purpose and is going to be set up the work at its optimum. Should there be issues down the line we offer a full aftersales service which is really important because as heat pumps become more prevalent in the market we see a gap in the market where guys are going to have to upskill. Until that happens we’re going to have to fill that place.
The Retrofit
So, the retrofit. Here’s the big thing, I had never done one of these retrofits myself. I have been brought in as a specialist for the heating and the ventilation on a project but never actually looking at the fabric / windows or air tightness. So, the big thing is, where do you start? It’s very daunting but don’t let the jargon overtake what you are trying to achieve. The reason we did it was because we bought a new house and we were looking to move into somewhere sort of sustainable for the future from a running cost point of view in the next 20/25 years.
I had to on this particular occasion not just consider the heating and the ventilation. I had to consider external wall insulation, internal wall insulation, what type of windows do I go for? Do I dig up floors? So, there is quite a bit going on. What I would say to anyone considering a retrofit is: very early on engage with a BER accessor who can do a technical assessment. These guys are really important to guide you through the process.
For anyone who doesn’t know who a BER Accessor is, these guys are basically independent energy auditors hat have to be registered with the SEAI. These guys are also in a great position to be able to offer you advise on grants, particularly now that grants have completely changed. One of he first questions I had was what grants are available other than the heat pump one, considering I was doing more than one measure. Another big thing to consider is how deep of a retrofit are you going with? The deeper the retrofit the more cost its going to entail to get to where you think you want to go.
The House

So, a little bit more about the house. The house is relatively new to be honest, 1995 construction, semi – detached house with a floor area of 125m2. The energy rating for the house was a D1. So, for anyone who doesn’t know what an energy rating is, it’s a sliding scale from G right up to A1. G being the poorest most inefficient, up to A1 which is the most energy efficient that you can get. So, we weren’t bad but we weren’t great either.
After doing the surveys when we were buying the house we realised quickly we would have to do all this work so we actually made the decision, and it wasn’t the intention at the time as we wanted to move into the house and do the work. As things progressed we made the decision not to move into the house and just go at all the measures together to try and get it done as quickly as possible.
The BER
We were dealing with an old boiler installed in 1995. Replacing that boiler wasn’t an option due to everything being so old. When we started out we wanted to achieve the best possible energy rating without spending a load of money. So, we started with the practical advice from Cian the BER accessor who did the technical assessment. Now the technical assessment entails a pre-BER and a post-BER. The pre-BER detailing the house as it is the moment without any measures completed to improve the quality of it. We were lucky in the sense we had bought the house so we had the BER done already. Hence the reason we knew it was a D1. The big thing was, when we engaged with the BER accessor so quickly we had a decision to make. Do we want to go to A1 and spend loads of money?
Our practical thing was, here’s our budget, this is what we have, how do we make it work as best as possible, because to be honest on something like this you can spend money and just keep going particularly with the way costs of materials are going at the moment. There were practical things as well – do we just look at the heating, do we change the windows, do we install solar PV. Little things that could have been done on their own but in terms of impact, would they have had a bigger impact for us down the line. As well as that we wanted to keep in mind the aesthetics of the house, we’re in a little cul-de-sac, there’s 28 houses, everything looks the same, so the last thing we wanted to do was change the colour of the house or go absolutely mad with different things.
So, in relation to the old BER we had an old oil boiler that was 27 years old. We had an analogue time clock which was basically the oldest of the old clocks and we’re not even sure if it was working. The double glaze window seals were starting to go. The windows were wooden frame and were starting to rot. So, as we got into it there was more and more things starting cropping up. The attic itself, the insulation was very very limited, 50mm insulation which by today's standards is exceptionally poor. The walls themselves were 3x2 battens with some insulation behind the plasterboard. The ventilation it was as old school as it comes, a hole in each bedroom and that was the vent. What we had to work with was very very limited. In terms of the scope, after engaging with Cian we knew we had to work from the start again.
So, based on Cian doing the technical assessment, this was the to-do list:
- Insulate the attic and walls
- Upgrade the Heating System, completely
- Introduce MHRV system
- Upgrade doors and windows
- Air tightness
Insulation
Unitherm as a company always take a fabric first approach. If your house was my old house, a 1995 build, with no measures completed on it and you said to us you wanted a heat pump, we as a company would come back to you and say have you considered any fabric measures – if you haven’t maybe you should.
The reason is: Heat pumps are very very efficient and a great source of heat in well insulated buildings. If they go into old buildings that aren’t insulated and aren’t optimised with heating controls they can actually be very very inefficient. This is a really important thing to point out.
So, when we looked at the insulation we had a couple of different options. It was either external wall insulation or internal insulated board. In terms of U-value we were really considering the 150mm external wrap, to kill all the cold bridging and in terms of the level of comfort it was just ideal. From a technical point of view, it is the preferred option. But because we have red brick at the front of the house and the main wall was only a gable wall we actually decided against it. Cost was a big thing – in terms of percentage uplift external wrap vs the internal dry lining there was probably a 45% increase to go with external wrap. From that point of view, it became the better option of the two based on the costs. As well as that in terms of the U-value the insulated plasterboard was only slightly more inefficient for a BER over the external wall wrap so in terms of the impact of the BER there was a negligible difference. We went with the internal dry lining. Basically, everything came off the wall to go back on again.
Windows
We had some seals that were gone and they were wooden frame. In terms of getting the heat loss down to a minimum we went from the old double glaze to a new aluminium triple glaze window where the U-value was just under 1. We also went with an aluminium frame, it wouldn’t have made sense to go backwards a buy wooden frame windows. Aluminium frame for longevity. In terms of life cycle anything from 80 to 100 years.
One thing we considered massively with the windows was certification. Any good, reputable window manufacturer will have a BBA certification or an IAB certification. This is really important for anyone that is going doing grant work. The SEAI will look for certification, so its important that if you are doing a retrofit, whoever is doing your windows, make sure you ask these questions from the start.
Heat Pump
In relation to the heat pump and the heating system, once we completed the fabric measures we were then able to work out where the heat loss was in conjunction with Cian. We had an initial floor area in the house of 125m2 and by doing a little bit of an extension and converting the attic our floor area jumped up to about 160m2. Even by adding the extra area on to the house we were able to get the heat load down to 6.8kW which is really good.
In relation to the heat pump there was a couple considerations here. You’ve got two different systems – a monobloc and a split heat pump. The difference between the two is a very simple within reason. A monobloc is a large unit that has all the components inside and you just run pipework into the house. The split system for all intense purposes is quite small but in terms of the indoor unit (the cylinder) its much bigger than what would be associated with the monobloc. The reason for that is the majority of the components to work the split system are actually in where the cylinder would be located, so that was a big consideration. We didn’t have a massive garden, so we went with a split system. Predominately for retrofits the attitude with most installers out there is to go with a monobloc, but space was a big consideration for us and we just physically didn’t have it. Also we were very mindful of our 2 young kids, so something like this in the back garden is just putting it out there and flashing lights for them to break it. We located it on cantilever brackets off the gable wall.
Now a consideration here for people is that if your looking at putting you heat pump on an external wall, if I was to wrap the house and use external wall insulation it wouldn’t not have been suitable. Be very mindful in terms of the process that you go through. You probably need to be a couple of steps ahead of what you need to do. Another big consideration is, because we’d spent so much on insulation and windows – the efficiency of the heat pump. The better the efficiency of the heat pump the better your helping the score of your energy rating.
Heat Emitter
Once the heat pump is sized, we then do a heat loss calculation per room. One thing we wanted to do but couldn’t was put underfloor heating downstairs and take up the floors but the cost associated with that was prohibitive. Ideally if we could afford it we would have done it. Again, this harps back to the conversation you have with your BER accessor or your technical assessor at the start. Do you want to spent, or not – there are things to consider. So, what we do for every house is we take the set of plans and we do a heat loss calculation per room to make sure the radiators are sized to get the optimum output per room. We so this for a number of reasons – we have to back it up with a calculation sheet because if you are going to the SEAI for a grant, we have to show that each radiator that goes in to any room, covers the heat load or loss for that room. That is paperwork the SEAI will look for. We do all this as standard with our designs. We’ll also given these calculations that as well in terms of rad sizes to locate where the radiators go in rooms.
Heating Controls
In relation to heating controls there now some grant available for retrofits from the SEAI. We had no heating controls previously. It was simple ‘On’ or ‘Off’.
We introduced zone control downstairs, zone control upstairs and zone control in the attic space. We went with a Heatmiser Neo thermostat. It’s very simple, the buttons are up or down to set the temperature or you can go more advanced and have an app on your phone and you can set the temperatures when your out of the house, allowing flexibility. The way we use it, its set to set point, up or down – when the room hits that temperature heating goes off. Very simple but in terms of the flexibility it meets all the regulations and requirements.
HRV
Like I explained earlier we had a hole punched through the wall in each room and that was the ventilation in the house. Because we were carrying out a load of ventilation measures and going to the extent we did, we blocked up all those air vents in the rooms and we introduced a mechanical heat recovery ventilation system.
What this system does is – we take a duct for fresh air and we supply room such as sitting rooms, living rooms, study’s and bedrooms. This is fresh air we take in through a pipe that supplies these rooms. Then as part of the system we have exhaust air outlets that would be in bathrooms, kitchens, utility spaces and what this system does is pull that air out from those areas, effectively creating a cycle. Pulling that fresh air that your getting ducted to your bedrooms, pulling it through and coming out through the bathroom, kitchen and utility areas. This air coming out passes through a heat exchanger, so the fresh air coming in isn’t cold. Its going through a heat exchanger, capturing the energy from the air – the kitchen space, the bathroom space so its pre heating that fresh air coming in.
We did consider another ventilation system which was DCV, but we wanted to bring the air tightness down as low as possible and DCV does mean having some wall vents.
Ventilation is very important but it might not be practical. If your going to the extent of pulling ceilings down it is probably something that should be considered. It does have a very positive effect on your BER as well. Like with the radiators, with HRV we have to do the calculations per room to make sure we’re not supplying too much fresh air and equally we’re not taking too much out, because you could have a cycling effect if you taking too much air out or putting too much air in. So again, for the SEAI we will actually do this as part of the course to submit with your paperwork.
Air Tightness
Air tightness is a really big thing. The measures we considered were tape around the windows, scratch coating areas that we couldn’t get with the paint, and actually then covering areas with Blower air tightness paint. This is to reduce the permeability of the blocks themselves. It’s an exercise that’s often overlooked but really helps in terms of your BER and your heat loss calculation.
The Result
We started off with very limited space, we were able to create more space. With the measures we were able to get the house comfortably within the A3 band. To achieve this, it was the air to water heat pump system, heating controls that we put in, triple glaze windows, attic insulation to a substantial level, wall insulation to a substantial level, full mechanical heat recovery ventilation and air tightness.
You can see there’s a big improvement. In terms of getting more of an uplift, had we gone with underfloor heating we still probably would have stayed in the A3 band. So, in terms of that cost to do the underfloor heating, that would have cost around €5,000 overall but we still would have stayed in the A3 band. Sometimes cost over the measure itself is something to be considered.
The only way we think we can get the house to an A2 is basically covering the roof with PV. Its primary energy and can be used locally in the house. Now we did consider putting PV on the roof, but simply because of costs running away with themselves we didn’t do it in the end.
Post BER
Once the Technical Assessment and the work is complete the Advisory Report will give you a summary of where you got to and the potential to go further.
Roofs – Rated Good, based on the potential of the house construction Good is the most it can be.
Walls – Good, had we put external wrap on and gone with 200mm wrap, we probably would have gone to a Very Good rating but again it’s a cost thing vs. what you’re getting back.
Windows – Very Good, so in terms of an uplift based on the SEAI methodology we can’t go any better in terms of what is done.
Floor – We didn’t touch because of cost.
Space Heating – Very Good, by replacing the oil boiler, gas wasn’t an option, by going with the heat pump we now have reached the same point as the windows where we can’t go any further in terms of the upgrade.
Water Heating – The heat pump is now doing the water heating, so again the SEAI treat that as a renewable source for hot water so in terms of the upgrade going further isn’t possible.
Renewables – A heat pump is classed as renewables. We could improve on that a little bit again by installing the PV but that’s a costing thing.
So, all in all we took it to an A3.
Annual Costs
We calculated the house was probably working out at €1,600 per year to run. Now just to bear in mind at the moment the cost rises happening with oil and gas and possibly electricity, (these figures were taken from the SEAI cost comparison tool for January 2022), so February is going to have a massive uplift.
In relation to the delivered energy costs, we think the house is going to cost just under €1,700 to run per year. We believe we will be able to take that down to €650 per year, based on the first bill we got for November to the middle of January. Our heating, electricity and hot water bill was about €250. So, a significant drop on what we expected. We think if energy costs were to stay the same, we’re fairly confident the €648 would drop again with the house being so well insulated. The space heating would have been about €1,200 on the old system, we’re going to bring that down to under €450. The hot water would have been about €423, We reckon we’ll bring that down to around €225. A substantial reduction in terms of running costs.
If I Had to Do This All Again…
It is a massive undertaking. What I would say is go with your gut. Trust your technical assessor – be clear with them from the very start – if your working to a budget, this is the budget. If budget isn’t an issue, let them off and see what they come back with. But I wouldn’t recommend that to anyone to be honest, but it is important now with what’s going on at the moment. What has changed since I’ve done this is the grants are substantially more than what they were when I was doing this. For instance, the grant for a heat pump used to be €3,500 and now based on the new scheme it is €6,500. So, a substantial increase on what was there previously. There’s also €700 for controls now so the SEAI are really backing the grants model because they’re seeing the whole thing that we need to upgrade our housing stock and upgrade it really quickly.
Unitherm
We are just the supply and design company but we have an installer network throughout the company and we can also help with people who are looking to go down the grant route by helping them with paperwork, advising them about various different schemes and really advise if its for them or not.
A big thing that we have that is completely different from everyone else, we have a team of engineers on the road, that should there be a problem down the line based on us supplying the system, that we will come out and we will assist in getting that system back up and running, which is a big thing that not many people are offering at the moment. We are also encouraging installers who haven’t done this before to come into our training centres in Cork and Galway and get trained on the products and upskilled. We don’t expect them to know it all but we’re here to offer technical advice and support and help them on that journey as well. This is a journey for everyone who’s doing a retrofit, and the guys doing the work. This is a massive exercise in everyone getting educated in retrofits.
On the heat pumps we offer three different brands. The reason is, no one manufacturer has a solution that fits all projects. So, we have different brands and we will tailor that to each of the brands. The same with the ventilation - we offer different manufacturers based on your project we’ll be able to offer a tailored solution.
If you are in the process of researching retrofitting your home, please get in touch with us or send us your technical assessment or BER. We can help you with any stage of the process and quote you for a heating system.